قالبگیری انتقالی رزین
( Resin Transfer Molding ( RTM
عناوین مورد بحث
- تعریف فرآیند
- مراحل انجام فرآیند
- مزایا و معایب فرآیند
- اجزاء فرآیند
- عوامل مؤثر در طراحی قالب
- روش های ساخت قالب
- اشکال مختلف RTM
تعریف فرآیند
قالبگیری انتقالی رزین فرایندی است که تحت فشار پایین و در قالب بسته انجام می شـود و برای تولید قطعات کامپوزیتی گوناگون و دارای ابعاد مختلف مورد استفاده قرار می گیرد. در اینجا با استفاده از انواع الیاف تقویت کننده و یک رزین ترموست قطعات کـامپوزیتی بـا دقـت ابعادی بالا و کیفیت سطح عالی تهیه می شوند. انواع رزین ها شامل اپوکسی، فنولیک، پلی استر غیر اشباع و وینیـل اسـترها در ایـن فرآینـد قابل استفاده می باشند. الیاف تقویت کننده نظیر الیاف شیشه، الیاف کربن و الیاف کولار و همچنین الیاف سنتزی بصورت مجزا یا در تلفیق با یکدیگر میتوانند استفاده شوند. نوع الیاف و رزیـن قیمـت و کـارایی مکـانیکی، شـرایط قـالبگیری و کیفیـت سـطح قطعـه را مشخص می نماید. علاوه بر مواد فوق الذکر بر حسب مورد مواد افزودنـی جهـت بهبـود خـواص ضـد آتـش و خمش و همچنین کیفیت سطح اضافه می گردد.
مراحل انجام فرآیند
- قرار دهی الیاف خشک با وزن معین درون حفره قالب.
الیاف تقویت کننده مورد استفاده می توانند بصورت یکی از حالات زیر باشند:
- binder-bound chopped mat
- random-continuous strand mat
- woven cloth format
الیاف می توانند طی یک پروسه جداگانه به شکل دقیق قالب در آمده (Preformed) و یا در هنگام قرار دهی در قالب با دست به شکل تقریبی حفره قالب درآیند. در صورت لزوم استفاده از ژل کوت می بایـد قبـل از قـرار دهـی الیـاف روی سـطح قالـب اسپری شود. اگر ژل کوت استفاده نشود سطوح قطعه کیفیت یکسانی خواهند داشت. Preformed استفاده شده نباید دارای ابعادی فراتر از حفره قالب یا قسمت آب بندی کننده قالب داشته باشد تا بتوان به سهولت قالب را بست و آب بندی نمود.
- پایین آوردن کفه دیگر قالب و بستن کامل آن و نگهداری آن با استفاده از گیره یا پرس.
- تزریق رزین و کاتالیست پیش مخلوط شده با نسبت معین به درون حفره قالب و آغشـته سازی الیاف موجود درآن ضمن خروج هوا از طریق منافذ (Vent) تعبیه شده در قالب. عمل تزریق رزین بمنظور اطمینان از پر شدن کامل قالب تا خروج رزین اضـافی از منافـذ ادامـه می یابد.
- توقف تزریق و آغاز پخت قطعه با استفاده از حرارت و … (از چند دقیقه تـا چنـد سـاعت متغیر خواهد بود)
- باز کردن قالب و خروج قطعه از قالب و ادامه کار برای تولید قطعه بعدی
- قطعه خارج شده میتواند جهت بهبود خواص پخت مجدد (cure post) شود.
در ذیل شمایی از فرآیند RTM نشان داده شده است
مزایای فرآیند
- امکان ساخت قطعات بزرگ
- امکان ساخت قطعات با عمق زیاد و شیب دیواره کم
- امکان قرار دهی الیاف در مکان های خاص
- قراردهی قطعات فلزی در قالب
- آلودگی کمتر
- کاهش جابجایی مواد اولیه و کنترل دقیق تر میزان آنها
- کاهش مصرف حلال
- تولید قطعات با دو سطح صاف
- اتوماسیون بیشتر
- صرفه جویی در نیروی کار و استفاده بهینه تر
- یکنواختی تولید
- کاهش سیکل قالبگیری و سرعت تولید بالا
- اقتصادی تر بودن
- قیمت قالبهای مورد استفاده نسبت به سایر روش های قالب بسته پایین تر است و زائدات کمتری وجود دارد.
معایب فرآیند
- طراحی و تهیه یک قالب دو کفه
جهت موفقیت آمیز بودن فرآیند لازم است تا قالب بصورت دقیق طراحی و سیستم باز و بسته کردن آن به درستی عمل نماید.
• نیاز به نیروی متخصص
• اقتصاد فرآیند
با توجه به سرمایه گذاری اولیه برای خرید دستگاه و ساخت قالب و …حداقل تعداد قطعات برای مقرون به صرف بودن فرآیند از سایر روش های قالبگیری تماسی بیشتر است (۵۰۰ – ۴۰۰ قطعه در سال)
اجزای فرآیند RTM
- دستگاه تزریق (Injectio Unit)
- نقش این واحد تزریق فرمولاسیون رزین به داخل حفره قالب تحت فشار مورد نظر می باشد. سیستم تزریق یا تک مرحله ای است و یا در دو مرحله ای انجام می شود. در دستگاه تک مرحله ای، رزین و پراکسید قبلا به میزان مشخص ترکیب شده و سپس با فشار تزریق می گردند. در دستگاه دو مرحله ای رزین و کاتالیست جداگانه پمپ می گردند و سپس قبل از ورود به قالب توسط یک مخلوط کن (Mixing Head) با هم به طور کامل مخلوط شده و سپس به داخل حفره قالب تزریق می گردند. از مزایای سیستم تزریق دو مرحله ای نسبت به گونه تک مرحله ای می توان به کاهش ضایعات رزین، قابلیت افزایش میزان کاتالیست در حین تزریق و سرعت بالای تولید اشاره نمود.
- قالب
- قالب RTM یکی از اساسی ترین بخش های آن است و برخی معتقدند که قلب فرایند است. هرگونه ایراد و اشکال در قالب منجر به بروز عیب و نقص در قطعه خواهد شد که رفع آن هزینه بر و دشوار است. لذا توجه به برخی معیارها و عوامل موثر در طراحی قالب ضروری است. بطور کلی میتوان گفت که اجرای موفقیت آمیز این فرآیند تا حد زیادی وابسته به داشتن یک قالب بی عیب و نقص و دارای طراحی صحیح است.
عوامل مؤثر در طراحی قالب RTM
- شکل و مشخصات قطعه
- تعداد قطعات مورد نیاز
- قیمت قطعه
- جاسازی قطعات دیگر در قالب
- مواد مورد نظر جهت ساخت قطعه
- محدودیتهای زمانی
- عمر قالب
- دقت ابعادی حفره قالب
- نحوه باز و بسته کردن قالب
- ضرورت گرم کردن قالب
- سفتی و وزن قالب
- کیفیت سطح قالب
- محل خروج هوا
یکی از مزایـای ذاتـی فرآینـد RTM پـایین بـودن فشـار تزریـق اسـت کـه از۱۰۰ psi بـالاتر نمی رود (کمتر از ۶ بار) فشار پایین تزریق باعث کاهش قیمت قالب می شود. علیرغم پایین بودن فشار تزریق، فشار ایجاد شده در درون قالب بالاست و لازم اسـت سـختی قالب در حدی باشد که دفرمه شدن آن و در نتیجه کاهش دقت ابعادی قطعه جلوگیری شود.
روش های ساخت قالب
- روش مستقیم: تراشکاری حفره قالـب و خـود قالـب از بلـوک هـای فلـزی و غیـر فلـزی (تراشکاری محفظه قالب با استفاده از CAM/CAD)
- روش غیر مستقیم: از یک مدل اصلی استفاده شده که سـطوح قالـب می تواننـد ریختـه گری یا لایه گذاری شـوند (رزیـن هـای تقویـت شـده بـا الیـاف و پلیمرهـای بـا قابلیـت ریخته گری)
- روش هیبربد: ریخته گری و سپس تراشکاری سطوح قالب برای رسیدن به دقت ابعادی لازم.
مواد مورد استفاده در ساخت قالب
در تعیین جنس قالب باید خواص مختلف مواد مورد استفاده را مد نظر قرار داد:
- خواص شیمیایی: (سازگاری با عوامل پخت، رزین ها و …)
- خواص فیزیکی: (هدایت حرارتی، ضریب انبساط حرارتی، دانسیته و …)
- خواص ساخت: سهولت ماشین کاری، جمع شدگی، دقت ابعادی قابل حصول
- سایر خواص نظیر دوام و قابلیت تعمیر
مواد متداول
رزین پلی استر دارای پوشش ژلی (جهت نمونه سازی و تولیـد قطعـات کـم و پخـت در دمای محیط)
- رزین وینیل استر یا اپوکسی (استحکام، چقرمگی و مقاومت حرارتـی بهتـری نسـبت بـه پلی استرها دارند و دارای جمع شدگی کمتری هستند. قالب هـای اپوکسـی دارای پوشـش ژلی وینیل استر قالب های مناسبی هستند و در دمای محـیط یـا بصـورت گـرم اسـتفاده می شوند.
- آلیاژ روی: قالب فلزی با قیمـت پـایین بـوده و دارای اسـتحکام و سـفتی نسـبتا پـایینی می باشد. عمر مفیـد آن از سـایر قالب هـای فلـزی کمتـر اسـت و معمـولا بصـورت گـرم استفاده می شود.
- آلومینیم ریخته گری: مستعد سطحی متخلخل اند و سطح آنا به سـهولت صـدمه می بینـد و معمولا بصورت گرم استفاده می شوند.
- فلزات با پوشش نیکلی: صافی سطح خوب داشته و عمر طولانی دارنـد(بـالای ۱۰۰۰۰۰ قطعه) مناسب برای تولید قطعات پیچیده بوده و به صورت گرم استفاده می شوند.
- فولاد: مناسب برای تولید بالا و پخت گرم
در جدول ذیل میزان تولید برای قالبهای با جنس متفاوت آورده شده است.
- قالب های ارزان از جنس اپوکسی بیشترین استفاده را برای تولید قطعات در حجم پایین تولید دارند. در این حالت تولید قطعات در حد چند هزار است.
- پیچیدگی قطعه تعداد قطعات را که می توان با یک قالب تولید نمود کـاهش می دهـد. ایـن بدلیل صدمه رسیدن به قالب هنگام قرار دادن preform است.
- رزین سطح داخلی دارای کیفیت بالاتر و در قسمت بیرونی لایـه هـای الیـاف شیشـه بـا رزین اپوکسی است.
- جهت دادن سفتی لازم به قالب سطح بیرونی آن با چوب تقویت می شود.
- کل ضخامت قالب حدود ۵/۲ سانتیمتر است.
- در صورت نیاز به گرم و سرد کردن باید در هنگـام سـاخت مسـیرهای مـورد نظـر را تعبیه نمود.
- بدلیل هدایت حرارتی پایین اپوکسی گرم یا سرد نمودن قالب طولانی است.
- در هنگام استفاده از قالب اپوکسی باید حتما از عوامل جدا کننده (واکس ها، سـیلیکون یـا پلی وینیل الکل) استفاده نمود. چسبیدن قطعه به قالب منجر به کندن رزیـن سـطح قالـب می شود.
- قالب های فلزی با آبکاری نیکل دارای کیفیت سطح بهتر قطعه، دوام بهتر، سـرعت گـرم و سرد کردن سریعتر و فشار قالبگیری بالاتر می باشند.
- برخی قالبها دارای یک کفه نیکلی و یک کفه اپوکسی هستند. در این حالت آب بندی بهتر انجام می شود. با دو کفه نیکلی بدلیل احتمال وجـود ناصـافی در حـین ماشـینکاری آب بندی مطلوب نیست.
- قالب های با دو کفه نیکلی دو تا سه برابر گرانتر از قالب های با یک کفه هستند.
- با توجه به امکان گرم کردن قالب تا دمای بالا بسیاری از رزین هـا را می تـوان اسـتفاده نمود.
- رزین ها کاتالیز شده با پخت دمای بالا بدون نگرانی از آسیب رسیدن بـه قالـب ناشـی از گرمای حاصل از پخت می توانند استفاده شوند.
- با توجه به دشواری اصلاح مکان های خروج هوا در قالب های نیکلی بهتر است ابتدا شرایط پر شدن قالب و مکان های خروج هوا در قالب اپوکسی آزمون شده و سپس قالـب نیکلـی آن ساخته شود.
- قالب های ریخته گری برای میزان تولید پایین کاربرد دارند. از آلیاژهای روی ، آلومینیم و فولاد می توان استفاده نمود.
- این قالب های بیشتر مزایای قالب های نیکلی را دارند و اصلاح مکان خروج هـوا و آب بنـدی آنها ساده تر از قالب های نیکلی است.
- قالب های ساخته شده از آلیاژ روی و آلومینیم غالبا دارای تخلخـل بـوده و ممکـن اسـت جهت جدا نمودن قطعه از آنها نیاز به هوا و رها ساز باشد.
- مزیت این قالب ها نسبت به نوع نیکلی عدم وجود تنش پسماند در آنها است که طول عمـر طولانی می دهد. قالب های نیکلی دارای تنش پسماند بودن و بتـدریج سـطح آنهـا تخریـب می شود.
- درصورتی که میزان تولید بالا باشد یا قالب های چند تکه پیچیده ای مـورد نیـاز باشـد از قالب های ماشینکاری شده فولادی باید استفاده نمود. در این قالب هـا مـی تـوان از پین هـای راهنما و پین های پران قطعه استفاده نمود و چرخه قالب گیری را کوتاهتر نمود. قیمت ایـن قالب بالا است ولی عمر آنها طولانی است و تا ۱۰۰۰۰۰۰ قطعه می توان بـا آنهـا تولیـد نمود.
دیگر عوامل مؤثر در طراحی و ساخت قالب
- ساختار قالب
- پین های راهنما
- سیستم باز و بسته کردن قالب
- سیستم کنترل دمایی
- محل تزریق رزین
- آب بندی قالب
- منافذ خروج هوای درون قالب
- سیستم پران قطعه
اشکال مختلف فرآیند RTM
(VARTM (Vacuum assisted RTM
در فرآیند VARTM از خلا در محل خروجی های هوا (Vent) استفاده می گردد. مزیت این روش آن است که حتی حباب های بسیار ریز هوا که در بین فیلامنت های الیاف بدام افتاده اند حذف می گردند و لذا میزان حباب حبس شده از حدود %۱ برای قطعات RTM به تقریبا صفر درصد می رسد. تفاوت بین این قالب و قالب RTM در استفاده از درزبندهای دینامیکی است. این درزبندها تو خالی هستند و قابلیت آن را دارند که هنگامی که قالب بسته می شود خلا اعمال گردد تا از آسیب به آن جلوگیری گردد (شکل ذیل) هنگامی که قالب بسته می شوند فشار باد کمی داخل آن اعمال می شود تا بتواند کاملا عمل درزبندی (Sealing) قالب را انجام دهد. همچنین از واشرهای V شکل نیز پیرامون قالب استفاده می گردد.
فرایند Light RTM
در این فرآیند مشابه فرآیند VARTM از خلا استفاده می گردد. قالب مورد استفاده در اینجا از لحاظ ساختاری قدری متفاوت است. در اینجا، کفه اول قالب مشابه فرآیند RTM – NORMAL می باشد اما کفه دوم آن نازک و شفاف است بگونه ای که می توان جریان رزین داخل قالب را دید. تزریق معمولا از پیرامون قالب صورت می گیرد. زمان پر شدن قالب حدودا سه برابر سریع تر از زمانی است که تزریق از نقطه وسط صورت می گیرد فشار تزریق پایین و در حدود ۰/۵ bar می باشد و لذا پر شدن از پیرامون، اندکی ضعف طولانی بودن زمان پر شدن قالب را بدلیل کم بودن فشار تزریق جبران می نماید. این فرآیند برای قطعات بسیار بزرگ و یا قطعات با تیراژ کم دارد، مناسب است.
فرایند RTM – MIT
فرآیند RTM یا قالبگیری چند پوسته ای ( Multi Insert Tooling ( RTM – MIT از اشکال جدید RTM بوده و برای تیراژهای بالاتر از ۲۰۰۰ عدد در سال مناسب است. در این فرآیند چندین پوسته که در واقع قالب اصلی هستند وجود دارد و به همراه کفه پایین قالب، دقیقا معادل کفه پایین قالب RTM – NORMAL می شود.
حدود دو سوم سیکل فرآیند صرف تمیز کاری قالب (کفه اصلی)، اعمال واکس و فیلم، ژل کوت، لایه گذاری الیاف و پس از بازکردن قالب دادن زمان کافی جهت پخت مناسب قطعات جهت جلوگیری از تغییر شکل می شود. در صورتی که در فرآیند MIT در تمامی این زمان ها صرفه جویی می گردد. لذا تمامی پوسته ها بیرون از قالب، تمیز کاری می گردند بر روی آنها ژل کوت اعمال می گردد و پس از سخت شدن ژل کوت، لایه گذاری الیاف صورت می گیرد. هر کدام از پوسته ها داخل قالب قرار می گیرند. تزریق صورت می گیرد و پس از ژل شدن قطعه، قالب باز می گردد و قطعه به همراه پوسته از قالب خارج می گردد. شمایی از این فرآیند در ذیل نشان داده شده است.
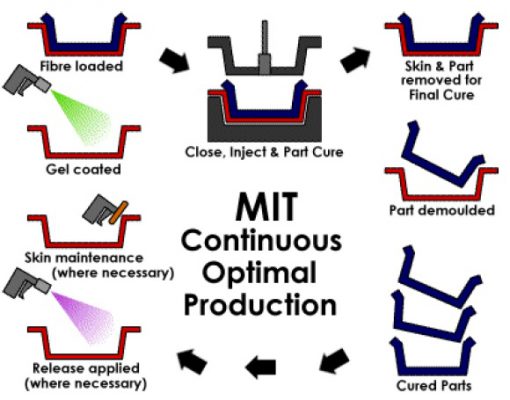
مراجع
- پلاستیک های تقویت شده ، محمد حسین بهشتی و امیر مسعود رضا دوست، انتشارات پژوهشگاه پلیمر و پتروشیمی ایران ۱۳۸۴٫
- سایت اینترنتی www.rtmcomposites.com
سوالات متداول
خلاصه ای از نحوه قالبگیری انتقالی رزین؟
در روش قالبگیری انتقالی رزین ماده تقویتکننده به صورت خشک به ابعاد موردنظر بریده میشود و یا به شکل موردنظر پیش شکل داده شده، درون حفره قالب قرار داده میشود. سپس قالب بسته شده و توسط گیرههایی یا به کمک پرس با فشار پایین، محکم بسته نگه داشته میشود. پس از آن رزین درون حفره قالب تزریق میشود و همزمان با آغشته کردن تقویتکننده، هوای درون حفره را عقب زده و قالب را پر میکند. زمانی که رزین اضافی از منافذ خروج هوا بیرون زد، تزریق رزین متوقف شده و پخت آغاز میشود. با کامل شدن پخت رزین ممکن است چند دقیقه تا چند ساعت به طول بیانجامد قالب باز شده و قطعه از قالب جدا میگردد.
مزایای روش قالبگیری انتقالی رزین کدام است؟
از مزایای این روش میتوان به امکان ساخت قطعات بسیار بزرگ، امکان ساخت قطعات با عمق زیاد و شیب کم، قرار دادن الیاف در مکانهای موردنظر و در نتیجه دستیابی به خواص بالا، امکان تولید چند قطعه یا یک قطعه به صورت یک تکه، امکان قرار دادن قطعات فلزی درون قالب، آلودگی محیطی کمتر، استفاده حداقل از حلال و اقتصادیتر بودن فرآیند اشاره کرد.
معایب روش قالبگیری انتقالی رزین کدام است؟
سرمایهگذاری اولیه برای طراحی و تهیه یک قالب دو کفه دقیق که باز و بسته کردن آن دقیق انجام شود ، نیاز به نیروی متخصص و با تجربه ، خرید دستگاه تزریق
در روش قالبگیری انتقالی رزین از چه نوع رزین هایی میتوان استفاده کرد؟
انواع رزین ها شامل اپوکسی، فنولیک، پلی استر غیر اشباع و وینیـل اسـترها در ایـن فرآینـد قابل استفاده می باشند.
با سلام و احترام چه مزیتی هایی در طی فرایند قالب گیری به انتقال رزین وجود دارد ؟
با سلام و احترام
مزیت هایی از قبیل امکان ساخت قطعات بزرگ،امکان ساخت قطعات با عمق زیاد و شیب دیواره کم،امکان قرار دهی الیاف در مکان های خاص،قراردهی قطعات فلزی در قالب،آلودگی کمتر،کاهش جابجایی مواد،اولیه و کنترل دقیق تر میزان آنها،کاهش مصرف حلال،تولید قطعات با دو سطح صاف،اتوماسیون بیشتر و …. دارا می باشد
سلام امکانش هست از قالب های سیلیکونی توی این روش استفاده کرد؟
خیر، از قالب سیلیکونی استفاده نمیشه
بیشتز از قالبهای فلزی ریختهگری و یا کامپوزیتی اسفاده میشه.